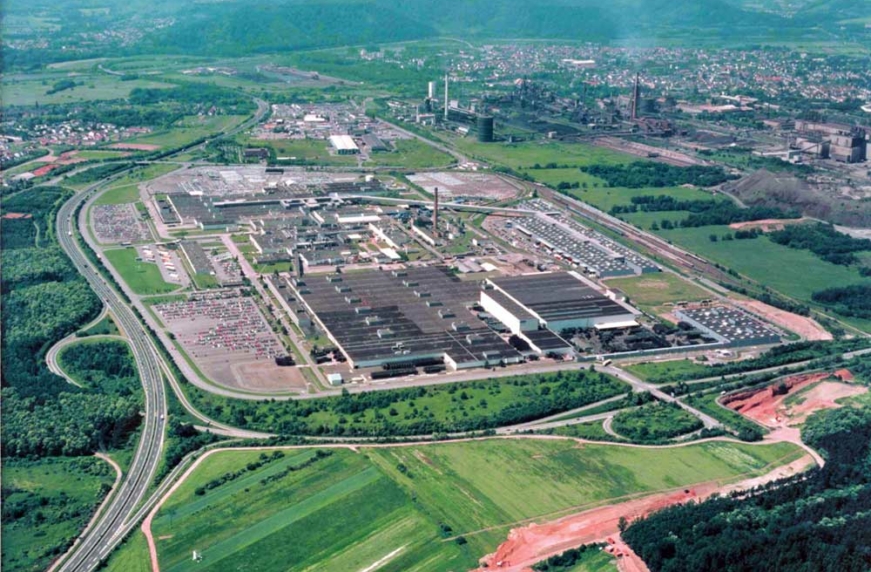
Завод Ford в Германии: Реконструкция качества
Компания Ford активно внедряет на своих предприятиях по всему миру унифицированную систему стандартизации и контроля качества. Мы ознакомились с ноу-хау во время экскурсии на главный европейский завод компании в Саарлуисе.
Компания Ford активно внедряет на своих предприятиях по всему миру унифицированную систему стандартизации и контроля качества. Мы ознакомились с ноу-хау во время экскурсии на главный европейский завод компании в Саарлуисе.
Жизнь небольшого города Саарлуис на северо-западе Германии кардинальным образом изменилась в сентябре 1966 года, когда здесь началось строительство нового завода компании Ford. С тех пор это предприятие выросло в несколько раз, а наряду со сборочным производством по соседству разместился индустриальный парк площадью 260 тыс. м кв., где находится 14 компаний-поставщиков, которые обеспечивают завод различными комплектующими. Предприятие Ford в Саарлуисе по праву считается одним из крупнейших машиностроительных комплексов в Германии.
Производственный процесс, в котором задействовано более тысячи роботов и 6,5 тыс. человек, позволяет при работе в три смены ежедневно собирать 1670 автомобилей нескольких моделей. Сегодня на предприятии выпускаются седан, универсал и 5-дверный хэтчбек Ford Focus, а также кроссовер Ford Kuga. В этом году к ним добавится «заряженная» версия Ford Focus ST. На заводе – четыре участка: штамповка, кузовное производство, покрасочный цех и финальная сборка. До 80% всей выпускаемой продукции отправляется на экспорт в более чем 80 стран мира, в том числе Австралию и Новую Зеландию.
![]() | ![]() |
Фордовский комплекс в Саарлуисе является одним из крупнейших в Германии. Здесь работает 6,5 тысячи человек. Ежедневно с его конвейера сходит 1670 новых автомобилей. |
Прессуем и формуем
Производство автомобиля начинается с прессовочного цеха, куда поставляется оцинкованная стальная лента. Листы подаются на несколько линий, где расположено 18 прессов с усилием до 6200 тонн. Там производится вырубка под размер и последующая штамповка до 400 различных элементов кузова. Всего прессовочный цех в состоянии обработать до 900 тонн металла в день.
От части к целому
Из прессовочного цеха штампованные детали транспортируются в цех производства кузовов, где они свариваются в готовый каркас. Кузовная линия – наиболее полно автоматизированная на предприятии. 98% всех операций выполняется 895-ю роботами. Сначала производится сварка деталей днища. Затем, в зависимости от модели и типа кузова автомобиля, свариваются боковые панели и крыша. Параллельно этому идет сварка дверей, капота и крыльев, которые навешиваются на готовый каркас кузова. Так каждые 30 секунд появляется полностью готовый кузов, который отправляется на следующий этап – покраску.
![]() | ![]() |
Комплектующие из индустриального парка поступают на конвейер по подвесным линиям. |
14 цветов
Для выпускаемых на предприятии автомобилей предлагается 14 различных цветов. Перед окраской кузов покрывается несколькими защитными слоями. В частности, при фосфатировании кузов погружают в ванну с раствором различных солей фосфора, и на его панелях образуется кристаллический слой металлофосфата. Это обеспечивает оптимальную грунтовку и коррозионную защиту. Длина участка фосфатирования достигает 240 м. В процессе задействовано 114 роботов. Первоначальная грунтовка наносится электролизным методом, путем полного погружения кузова в ванну с грунтом. Разница в электрическом потенциале между кузовом и стенками ванны способствует прочной и однородной грунтовке поверхности, включая скрытые полости. Все внутренние и наружные швы закрывают специальным герметиком. Чтобы ограничивать распространение шума и вибраций, внутри кузова клеятся битумные подложки. На днище наносится несколько слоев защитного покрытия из эластичного пластика, а после этого кузов отправляется в покрасочную камеру. Кроме того, предприятие в Саарлуисе – единственный европейский завод Ford, где производятся и окрашиваются бамперы. Ежедневно здесь выпускается до 4500 бамперов, которые, помимо «родного» завода, отправляют на другие предприятия компании.
Финальная сборка
Из цеха окраски кузова и бамперы поступают на линию финальной сборки. На сборочной линии длиной примерно 2,8 километра кузов получает недостающие элементы – силовые агрегаты, ходовую, стекла, двери и детали интерьера. Они подаются в цех по огромному конвейеру из расположенного по соседству индустриального парка. Кроме того, ежедневно около 200 грузовиков доставляют на завод различные комплектующие. Всего на сборочном производстве используется до девяти тысяч различных деталей. Каждый день с конвейера сходит 1670 автомобилей. После всесторонней проверки они отправляются на стоянку готовой продукции, а оттуда поступают к покупателям по всему миру.
Качество с обратной связью
Кризис в автомобильной отрасли заставил многие компании провести оптимизацию технологических процессов, чтобы повысить конкурентоспособность выпускаемой продукции. В компании Ford приоритетным направлением в этой области стало внедрение четыре года назад новой системы контроля качества на всех предприятиях и производствах по всему миру. Она предполагает детальный статистический учет всех неполадок и обращений клиентов, а также обработку информации. Для этого была разработана унифицированная система отчетности и технической документации, которая используется на предприятиях во всем мире. Она позволяет фиксировать малейшие отклонения и выявлять проблемы на каждом участке – от прессовочного производства до финальной сборки. Каждое утро мастера участков проводят брифинги, где рассматриваются возникшие проблемы и обсуждаются методы их решения. Быстродействие системы позволяет устранить мелкие недостатки в течение суток, а при обнаружении серьезных нарушений на решение проблем требуется не более трех дней. Внедрение новых стандартов позволило компании Ford существенно повысить качество выпускаемых автомобилей.
История завода в Саарлуисе
Строительство завода стартовало в 1966 году. 20 октября 1969 года на заводе собрали первый автомобиль – Ford Escort, а в 1970-м началось серийное производство модели; за 18 лет тираж Escort составил более 6,5 млн. экземпляров. Год спустя наладили сборку купе Ford Capri (1971–1975). Здесь же выпускались другие популярные модели – Ford Fiesta (1976–1980) и Ford Orion (1983–1993). В 1990-м компания отметила выпуск в Саарлуисе 5-миллионного автомобиля. В августе 1998 года началось производство первого поколения Ford Focus. В 1998-м он сменил на конвейере Escort и с тех пор изготовлен тиражом более 10 млн. Одновременно с этим на территории завода был основан индустриальный парк, где разместились поставщики комплектующих. Миллионный Focus выпустили в 2001-м, а через два года на заводе изготовили 3-миллионный экземпляр модели. Кроме того, 2003-й стал годом запуска в производство компактвена Focus C-Max первого поколения. 10-миллионный автомобиль был изготовлен в Саарлуисе 1 июля 2005 года. Им стал 1,6-литровый Ford Focus с кузовом универсал. В марте 2007 года стартовало производство C-Max нового поколения. В феврале 2008-го с конвейера сошел первый кроссовер Kuga. В августе 2010-го на заводе собран 12-миллионный автомобиль. Запуск Ford Focus потребовал 300 млн. евро инвестиций и создания в Саарлуисе 500 новых рабочих мест.